magnetar68
Guest
I posted this in a couple other places, but I am thinking some of you guys here may have already done something similar. Below are pictures of my DIY LEDs and my proposed covers (dimensions included at the bottom):
1) What thickness acrylic should I use for the black bottom and clear splash protector? I was thinking 1/4" for the holes and 1/8" for the clear plastic splash protector.
2) Should I use a clear top? Any special type of acrylic for this since I want it impeding the light transmission as little as possible?
3) What is the best way to cut these 1.75" holes? I am worried about:
a.) Cracking the acrylic since these holes are somewhat close together
b.) The last few times I have drilled acrylic with a holes saw and a drill, the edges did not look great. I sanded them with a dremel grinding stone, but they still did not look great. Any tips?
4) What is the best way mounts these. I assume spacers and screws tapped into the block, but what types?
a.) rubber spacers? Aluminum? Where can you get these?
b.) what size machine screw? #6?
c.) what type screw? Aluminum to reduce corrosion potential?
[/QUOTE]
1) What thickness acrylic should I use for the black bottom and clear splash protector? I was thinking 1/4" for the holes and 1/8" for the clear plastic splash protector.
2) Should I use a clear top? Any special type of acrylic for this since I want it impeding the light transmission as little as possible?
3) What is the best way to cut these 1.75" holes? I am worried about:
a.) Cracking the acrylic since these holes are somewhat close together
b.) The last few times I have drilled acrylic with a holes saw and a drill, the edges did not look great. I sanded them with a dremel grinding stone, but they still did not look great. Any tips?
4) What is the best way mounts these. I assume spacers and screws tapped into the block, but what types?
a.) rubber spacers? Aluminum? Where can you get these?
b.) what size machine screw? #6?
c.) what type screw? Aluminum to reduce corrosion potential?
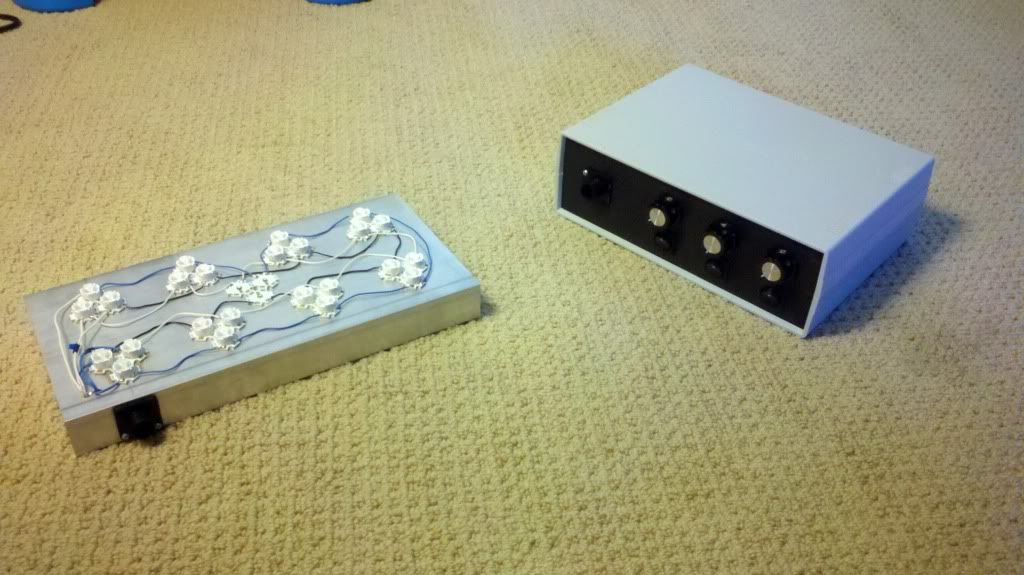
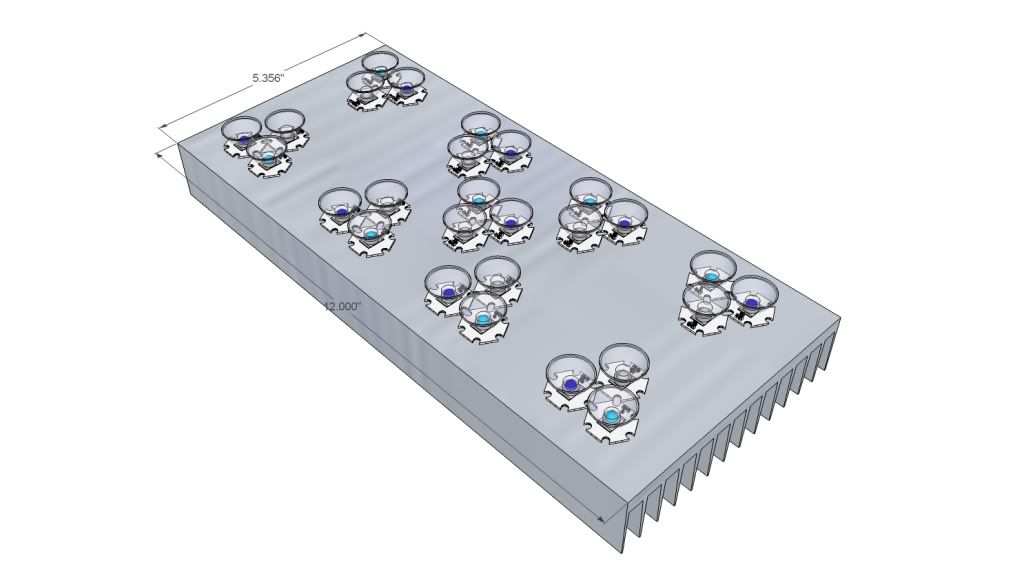
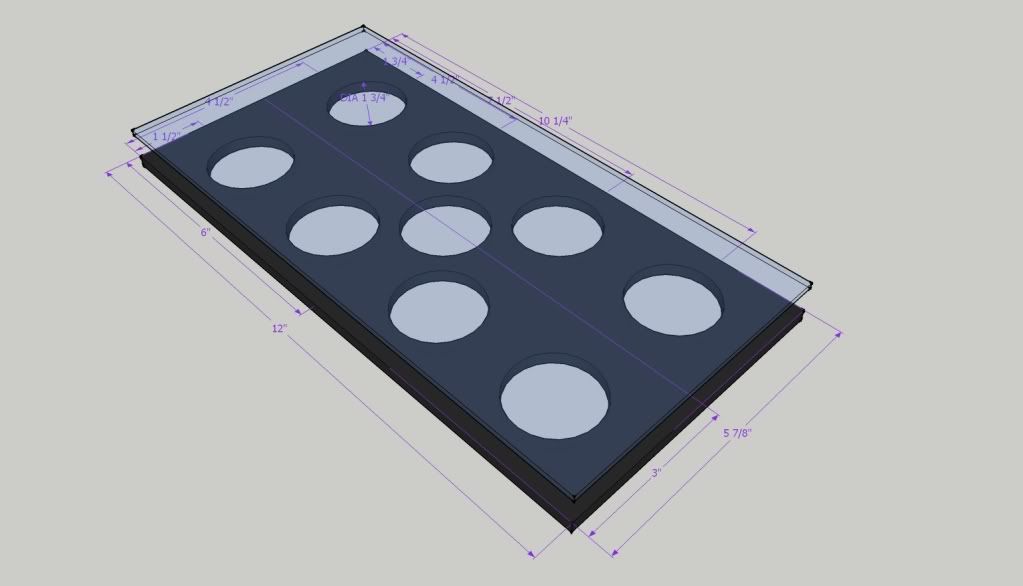
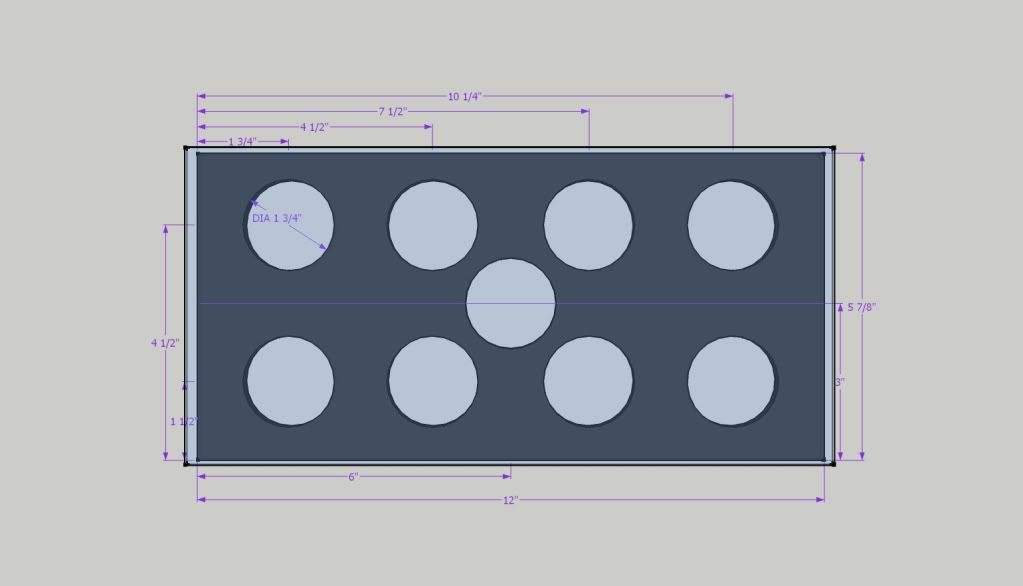